How to choose thermal spray powder- part3 ceramic
Home » December 2021 » Archives for 2021-12-08
How to choose thermal spray powder- part3 ceramic
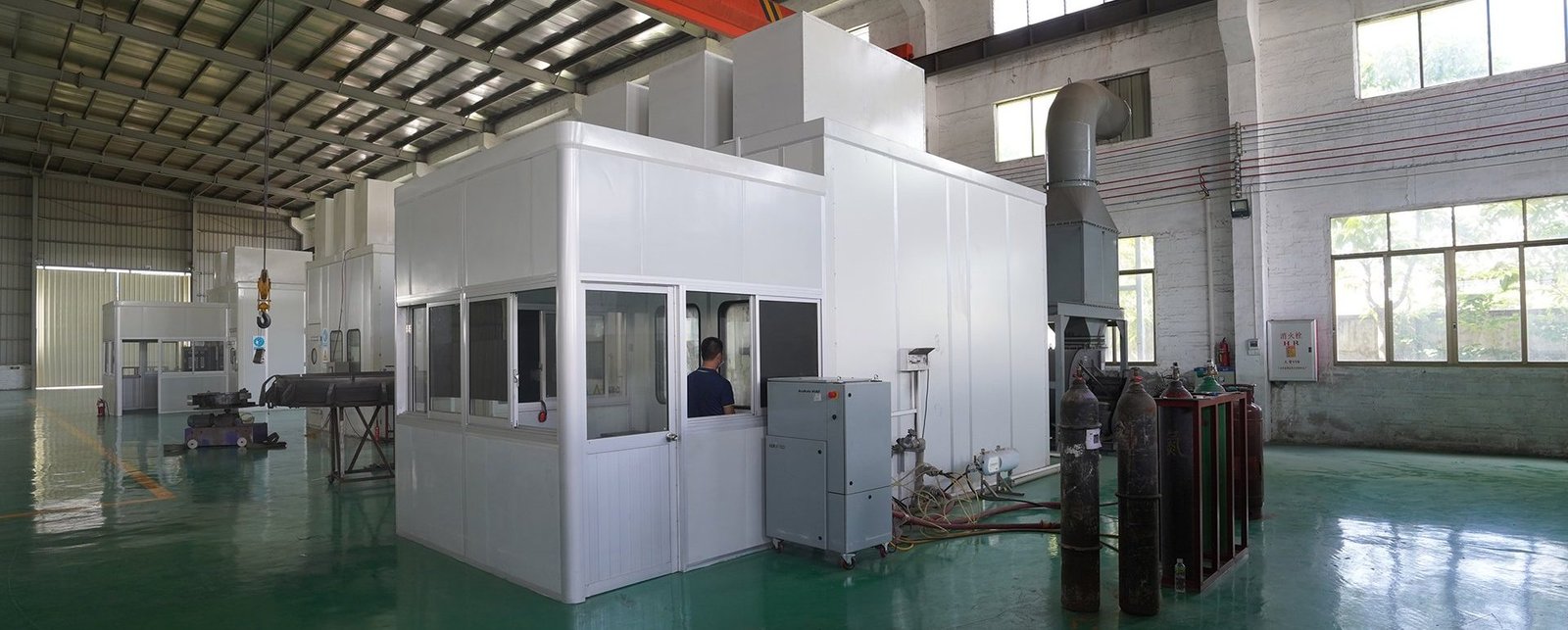
Selecting the right material is the priority condition for successful thermal spraying coating application on the workpiece surface. APT can help you choose the most suitable material for your application from our wide range of high-quality material products.
1 Classification of thermal spraying powders.
MetalsPure:
Cu, Al, Zn, Ni, Fe, Mo, W, etc…
Alloys: CuAl, NiCr, NiAl, NiAlMo, NiCrSiB, Steels, etc…
Super alloys: MCrAlY, Inconel, Stellite, Tribaloy, Hastelloy, etc..
Ceramics
Al2O3 based, TiO2 based, Y2O3 based, Cr2O3 based, ZrO2 based.
Carbides
Tungsten carbides: WC-CoCr, WC-Co, WC-Cr3C2-Ni, WC-Ni, WC-CoCrNi, etc..
Chrome carbides: Cr2C3-NiCr, Cr3C2-NiCrMoNb, etc…
Abradables
AlSi-Polyester
Basic properties and manufacturing process of thermal spraying powder- ceramic powders section.
1 Aluminum oxide based powders
* Most of the AL2O3 powder are Sintered manufacturing process, some are made by fused.
* Chemical composition of powder: Pure Alumina; Al2O3-3TiO2; Al2O3-13; Al2O3-40TiO2
* Good for abrasion, erosion, and sliding wear
* Good in alkali and acid environments
* Excellent dielectric properties
* Can be used between 843 to 1649 C
* Less TiO2, softer, and less resistance to chemicals
2 Chromium oxide based powders
* Reacted and sintered, composite will be used in the manufacturing process of CRO powder
* Chemical composition of powder: Pure Cr2O3. Which can be produced a hard , dense wear resistance coatings. The Cr2O3 coating can be insoluble in acids, alkails and alcohol. Can be used in the environment temperature of 540℃.
* Pure Cr2O3 coating has excellent engraving properties
* Cr2O3-SiO2-TiO2 has similar properties to CR2O3, and resists impact better than Cr2O3
3 Aluminum oxide based powders
* The manufacturing process including: Fused, Agglomerated and sintered
* ZrO-22MgO, with good thermal barrier properties and resistance to molten metals, has good particels erosion resstance, can be used up to 927℃
* ZrO-8Y2O3, excellent thermal barrier properties and stabilizes during spraying process. Can be used up to 1343℃
* By changing the composition of yttrium oxide, the service temperature changes and the spraying process is more stable.
As mentioned at the beginning, the correct selection of powder is the key to successful coating application. However, the selection of powder is indeed a very complex process. Without enough experience and theoretical basis, it is difficult to choose a very suitable powder. The factors we should consider include but are not limited to:
*The manufacturing level of powder suppliers;
*Powder manufacturing process, mechanical crushing, sintering, atomization and agglomeration, etc;
*Characteristics of spray gun, such as sg100 spray gun of Praxair and F4 spray gun of Metco.
*In practical application, the spraying powder parameters need to be adjusted according to the characteristics of spray gun; Size, material and other characteristics of the workpiece.
APT does not produce powder, but the experience accumulated in coating application for a long time enables us to find suitable powder among many factors and obtain successful coating application.
Therefore, whether you need us to spray coating for your parts, recommend a suitable powder for you, or provide an overall coating solution for your parts, you can contact us immediately.
## Our contact information is:E-mail Fchen@APTcoating.com
For more information about powder selection, please click to continue browsing.
# Ceramics
# Carbides
# Abradables
# Metal or alloy